Why Heat Distribution Matters More in Large Powder Coating Ovens
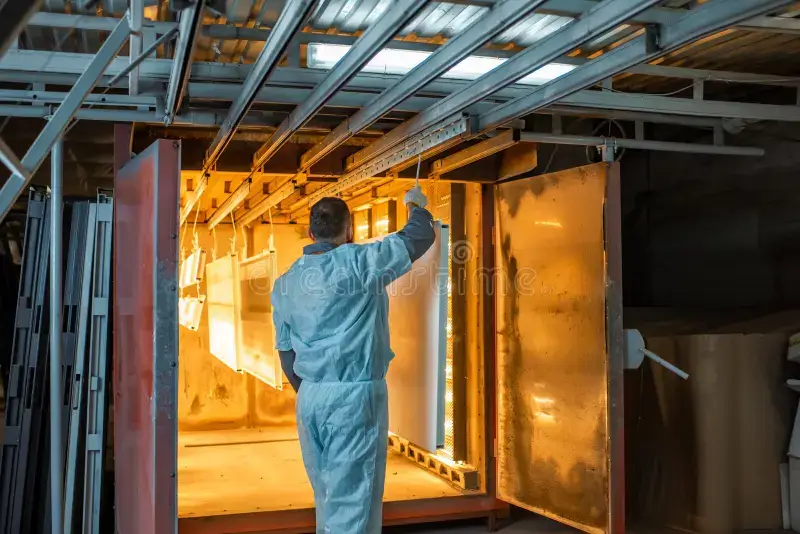
When it comes to large powder coating ovens, heat distribution isn’t just a technical detail—it’s the key to quality. Picture this: a massive chamber filled with different metal parts, each needing to be evenly cured with a layer of powder coating. If the heat isn’t distributed properly, some areas might end up perfectly cured while others fall short, leaving the coating uneven. Heat distribution becomes even more critical as the size of the oven increases, given the complexity of maintaining consistent temperatures. Let’s break down why achieving balanced heat matters so much in these larger systems.
Reaching Every Nook in Larger Chambers
In large powder coating ovens, it’s a challenge to ensure heat reaches every nook and cranny. These expansive chambers are designed to handle bigger parts or larger batches, which means they come with more corners and crevices where heat needs to travel. If heat doesn’t flow evenly throughout, certain areas of the oven—and the parts inside—might not receive the required temperature levels.
When heat doesn’t reach all parts of the oven, the powder coating can end up looking patchy or incomplete. This not only affects the appearance of the finished product but can also compromise its durability. Proper airflow systems and strategically placed heat sources are essential in these larger ovens to make sure the heat reaches every part of the chamber, ensuring that the coating is uniform throughout.
Consistent Curing Across Vast Surface Areas
Consistent curing is a fundamental part of using powder coating ovens. In larger ovens, the surface area being heated is significantly bigger, making it more challenging to maintain uniform heat. If one section is hotter than another, the powder on those parts may cure at different rates, leading to an inconsistent finish. This can be especially noticeable when dealing with oversized items or multiple items in a single batch.
The size of the oven doesn’t just mean more space; it means more potential for variations in temperature. High-quality powder coating ovens are designed to maintain consistent temperatures across the entire chamber, ensuring every part of the metal gets the same treatment. This consistency is key for both appearance and longevity, giving the coated items a more polished and durable finish.
Avoiding Cold Spots in Expansive Oven Spaces
Cold spots are a common issue in larger powder coating ovens. These are areas within the oven where the temperature remains lower than the desired curing level, often due to inadequate heat distribution. Cold spots can cause sections of the powder to cure improperly, leading to a finish that’s rough, uneven, or even prone to flaking over time.
To combat cold spots, oven manufacturers design systems that direct airflow more efficiently. Some ovens utilize multiple heating elements placed strategically throughout the chamber, ensuring a more even spread of heat. This method helps to eliminate cold spots and ensures that the entire batch, no matter where it’s positioned inside, gets the proper level of heat for thorough curing.
Uniform Layering of Powder Even on Bulkier Items
Large powder coating ovens are often tasked with coating bulkier items, like automotive parts or heavy machinery components. These items have irregular shapes, thicker metal, and sometimes varying thicknesses within the same piece, making even heat distribution vital. The challenge lies in ensuring that all parts of these larger items receive the same amount of heat, allowing the powder to melt and fuse uniformly.
If the heat isn’t distributed evenly, some sections of a bulky item might end up with a thinner coating or a different texture. Properly calibrated ovens ensure that heat wraps around every surface of the item, creating a uniform layer of powder. Advanced ovens often use convection heat to achieve this wrap-around effect, promoting even curing on larger or oddly shaped parts.
Balancing Heat Load to Prevent Uneven Baking
Balancing the heat load is a major factor in the performance of larger powder coating ovens. The concept is simple: the more evenly the heat is balanced throughout the oven, the more evenly the coating will cure. In a large chamber, it’s easy for heat to accumulate more in one area than another, especially if racks or parts block airflow. This imbalance can cause some areas to overheat while others remain undercooked.
Oven operators can manage this balance by adjusting the placement of parts and utilizing ovens with advanced airflow designs. Proper loading techniques also play a role in balancing the heat load. By positioning items correctly, operators can ensure that the hot air flows evenly, preventing any section from becoming too hot or too cold. This results in a smooth, even coating across all parts.
Managing Heat Flow for Multiple Racks and Batches
Larger powder coating ovens often handle multiple racks or batches at the same time, which adds another layer of complexity to managing heat distribution. When several racks are involved, ensuring even heat flow to each batch is crucial. If one rack gets more heat than another, it can lead to inconsistent results across batches, with some parts curing well while others remain undercooked.
To address this, many large ovens come equipped with zoned heating systems that allow operators to control temperature in different sections of the oven. This makes it easier to adjust the heat based on the position and size of each rack, ensuring consistent results no matter the load. Managing heat flow effectively in this way allows for efficient batch processing without sacrificing quality, making these ovens a valuable asset for high-volume production.